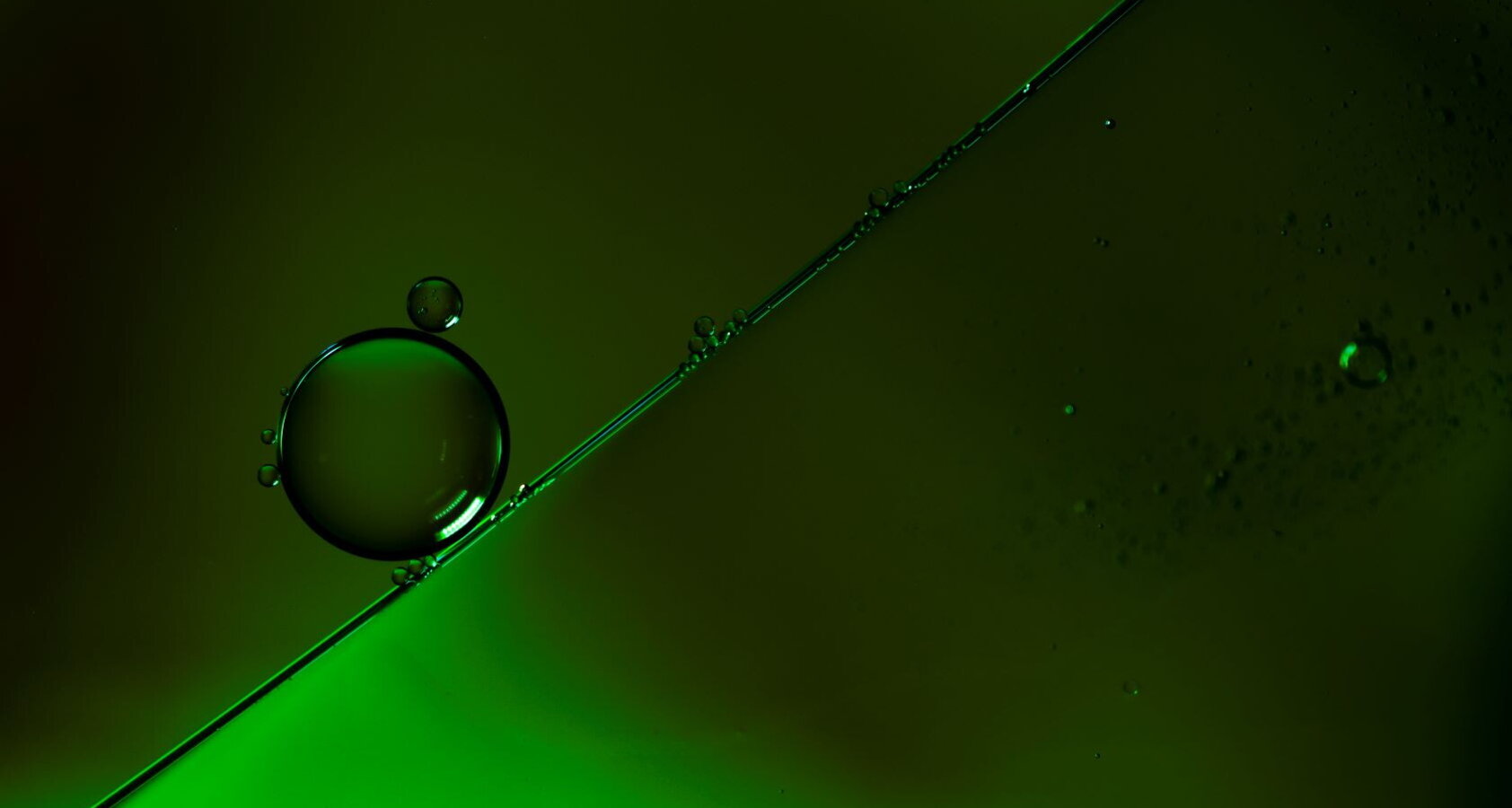
A new ally
A difficult alternative
The production costs of green hydrogen are still too high, especially when compared with those of natural gas, which means that it is not currently a real option for decarbonizing industries.
8 minT
he history of mankind is marked by our knack for turning nature’s matter into useful things. Ever since the discovery of fire, humans have burned wood to create light, heat, cook food, and defend against animals. Over time, this chemical processing of fuel became more sophisticated, allowing for the extraction of metals, the baking of clay, and the making of glass. The discovery of fire dates back about 2 million years, while the Bronze Age began around 5,000 years ago.
Since then, human history has undergone significant changes, with technological and social revolutions accelerating to bring us to the present day. We now consume enormous amounts of energy to sustain a world population that has grown from fewer than 100,000 when we discovered fire, to 10 million in the Bronze Age, to 8 billion today. Our civilization is built on material structures shaped using large amounts of energy. Although today’s methods are more sophisticated, the essence remains the same: we are still burning fuels to generate heat and transform matter.
Energy-intensive sectors
Metals, which are found in the minerals covering the Earth’s surface, exemplify the process of turning raw materials into useful products. These minerals, sometimes abundant and sometimes dispersed, are separated from oxygen and rock and then heated with coal until they become molten. Similarly, glass is made from sand, which melts at temperatures above 1,500 degrees Celsius. Cement is produced using limestone and clay, while ceramics are made by baking clay, and paper is created by pulping wood at high temperatures. Initially, we made these materials in rudimentary ways, but techniques and qualities have improved with the use of fossil fuels: coal, oil, and gas.
Iron is a prime example. The transition from simple cast iron—a low-quality iron that could withstand neither high temperatures nor pressure—to steel, which is refined with less oxygen and more carbon, revolutionized material production. Steel’s development allowed the construction of high-pressure-resistant pipes, enabling the drilling of oil reserves trapped at previously unreachable depths. The abundance of fossil energy also revolutionized chemistry and petrochemistry, leading to the production of fertilizers. This, along with the internal combustion engine and gasoline, exponentially increased agricultural yields, providing more food for billions of people.
Industries such as cement, chemicals, paper, glass, and ceramics consume vast amounts of energy, mostly from fossil fuels, to produce increasingly sophisticated products. Coal is used extensively in steel production to oxidize and extract iron from ore or to burn limestone to make cement. Natural gas is used in the production of ceramics, glass, and paper. These sectors face significant challenges in moving away from fossil fuels to reduce CO2 emissions, which is why they are referred to as “hard-to-abate.”
The suggestion of green hydrogen
Replace gas and coal with what? Hydrogen—the “green king,” of course—produced by electrolysis of water, separating it from oxygen using electricity generated from renewable sources. The idea of green hydrogen is appealing for European policy, which aspires to lead the green transition and achieve total decarbonization of the economy. The goal is to lead by example and foster innovation that can be exported globally, similar to the impacts of the first and second industrial revolutions.
However, significant challenges remain. Producing green hydrogen from water with renewable electricity is complicated worldwide, including in Europe. Transporting and storing hydrogen requires difficult-to-obtain materials. Currently, producing renewable electricity in Europe, even after decades of growth and subsidies, costs between €50 and €100 per megawatt-hour (MWh). This wide range depends on factors such as solar irradiation, wind speed, local opposition, and the feasibility of building large plants to achieve economies of scale. In recent years, the lower threshold has been abandoned due to increases in raw material costs. Even at €50 per MWh, producing 0.6 MWh of hydrogen from one MWh of green electricity results in a cost of €83 per MWh just for electricity.
Additionally, the cost of electrolyzers—machines that separate distilled water into oxygen and hydrogen—adds another €50 per MWh, with potential uncertainties on the upside. Special storage systems are required, made of metals that can withstand hydrogen’s aggressive properties, as hydrogen molecules are the smallest in the universe and tend to bind with others. Producing hydrogen also requires a lot of high-quality water—at least 10 liters for every kilogram of hydrogen, which must be distilled. Often, areas with abundant renewable energy, particularly solar, lack water. Conversely, areas with water often rely on desalination, which consumes significant energy.
Combining all these factors, the cost of green hydrogen easily reaches €180-200 per MWh. Early experimental projects in Europe have shown even higher costs, up to €400 per MWh. This explains why, five years after the Green Deal Commission took office in 2019, there are no green hydrogen plants or industrial plants using green hydrogen. The paradox is that many industries describe their plants as “hydrogen ready,” patiently waiting for this hydrogen utopia to become viable.
Cost comparison
The cost of hydrogen must be compared with the price of the most widely used fuel in hard-to-abate sectors: natural gas. In mid-2024, the price of natural gas in the European market—the most expensive globally—stands at €35 per MWh, while in the United States, it is around €9 per MWh. Worldwide production costs range from €5 to €10 per MWh, with significant reserves yet to be discovered and developed. The price of coal, used for steel and cement production, has doubled in recent years but still does not exceed €15 per MWh.
Currently, the costs of green hydrogen to replace fossil fuels are prohibitively high. However, if we aim to save the planet and eliminate CO2 emissions, the greatest burdens should be borne by those who consume the end products. For instance, the cost of one ton of primary steel could double from €700 to €1,400 per ton, which translates to an additional €0.7 per kilogram. For a pan made with greener steel, which used to cost €20, the extra cost would be just €1. This is not much of a sacrifice to save the planet.
Despite these good intentions, tariffs and taxes have never achieved technological revolutions or broken the link between material production, modernity, and fossil fuels