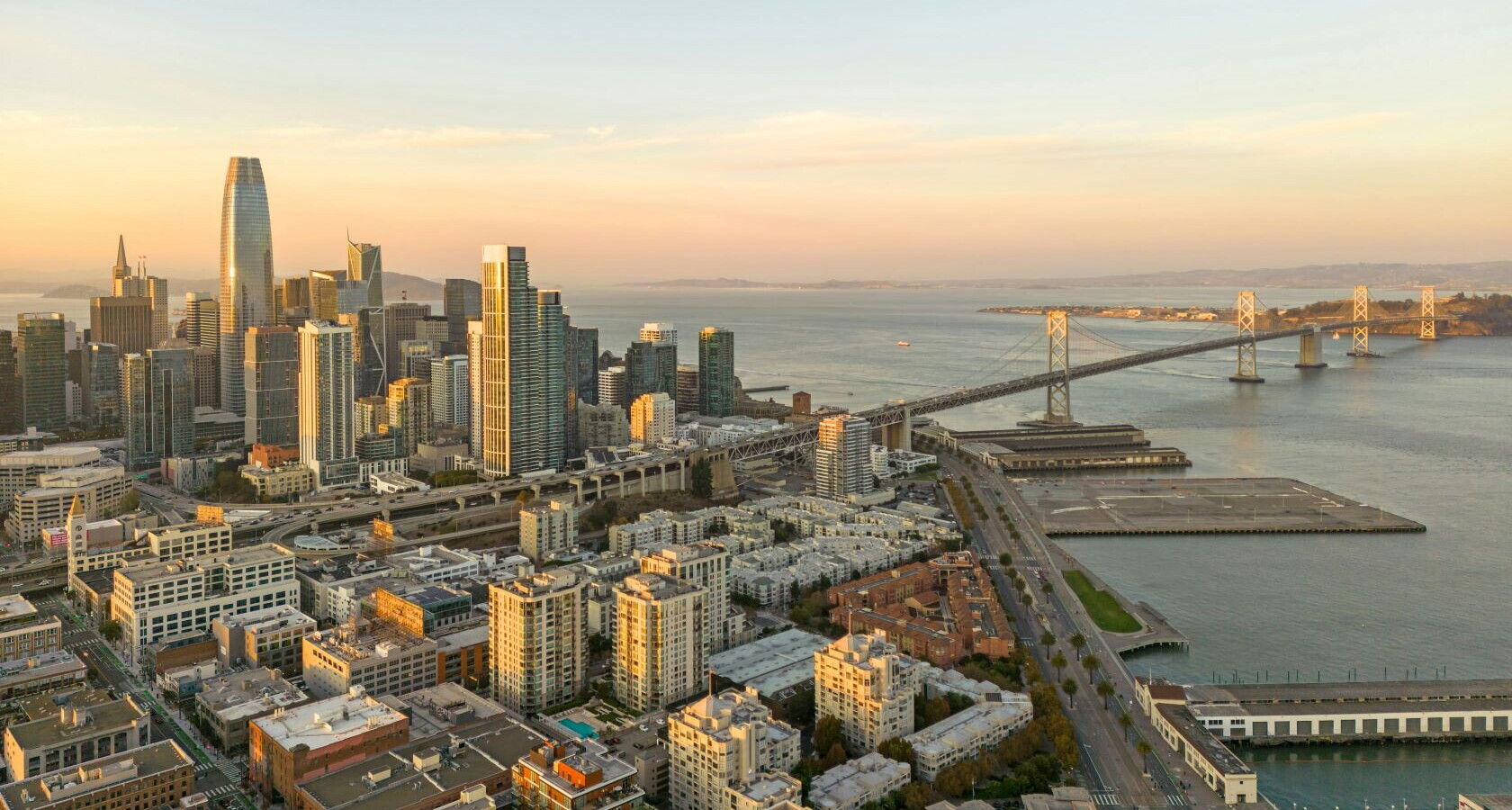
Strategies
Heavy industry & CO2 the challenges
Heavy industry accounts for 75 percent of industrial emissions. To reduce them, we need efficiency, alternative technologies and effective emissions markets. A comprehensive approach should balance economic development and environmental sustainability.
10 minI
ndustrial applications are globally responsible for 9 Gt of CO2: around one quarter of all climate-changing emissions related to energy consumption. The most significant contributions are related to heavy industries, particularly steel (2.6 Gt of CO2), cement (2.4 Gt of CO2) and petrochemicals (1.3 Gt of CO2). These three sectors alone account for nearly 75 percent of industrial emissions.
To estimate future emissions and to evaluate decarbonization strategies, focus on two parameters: the volumes of material produced in these sectors and the specific CO2 emissions per ton produced (Charts 1 and 2). The International Energy Agency’s Net Zero Emissions scenario predicts material production in 2030 to be broadly in line with current production. Specific emissions per unit of output, which have remained fairly stable in recent years, are therefore expected to decrease significantly by 2030 to come into line with any decarbonization scenario. Moreover, even if global volumes remain constant, it is important to remember that variations in some countries can be significant: for example, steel production in developing countries increased by 25 percent between 2016 and 2022.
CO2 emissions from these industries arise largely from the consumption of fossil fuels (mainly coal and natural gas) for high heat production, but in some cases they are also process emissions, as in the case of cement, where about half of the emissions are related to the chemical production process. To reduce emissions in these sectors, we need to focus on three approaches: more efficient use of the materials produced (to reduce the need for them), migration to alternative production sources and technologies, and increasing the efficiency of production processes.
Use of materials
Economic development and population growth, though slower than in the past, are closely tied to increased consumption of materials like cement and steel. These materials play a crucial role in various sectors, particularly construction. The demand for these resources is especially significant in developing countries, where investments in new infrastructure drive consumption.
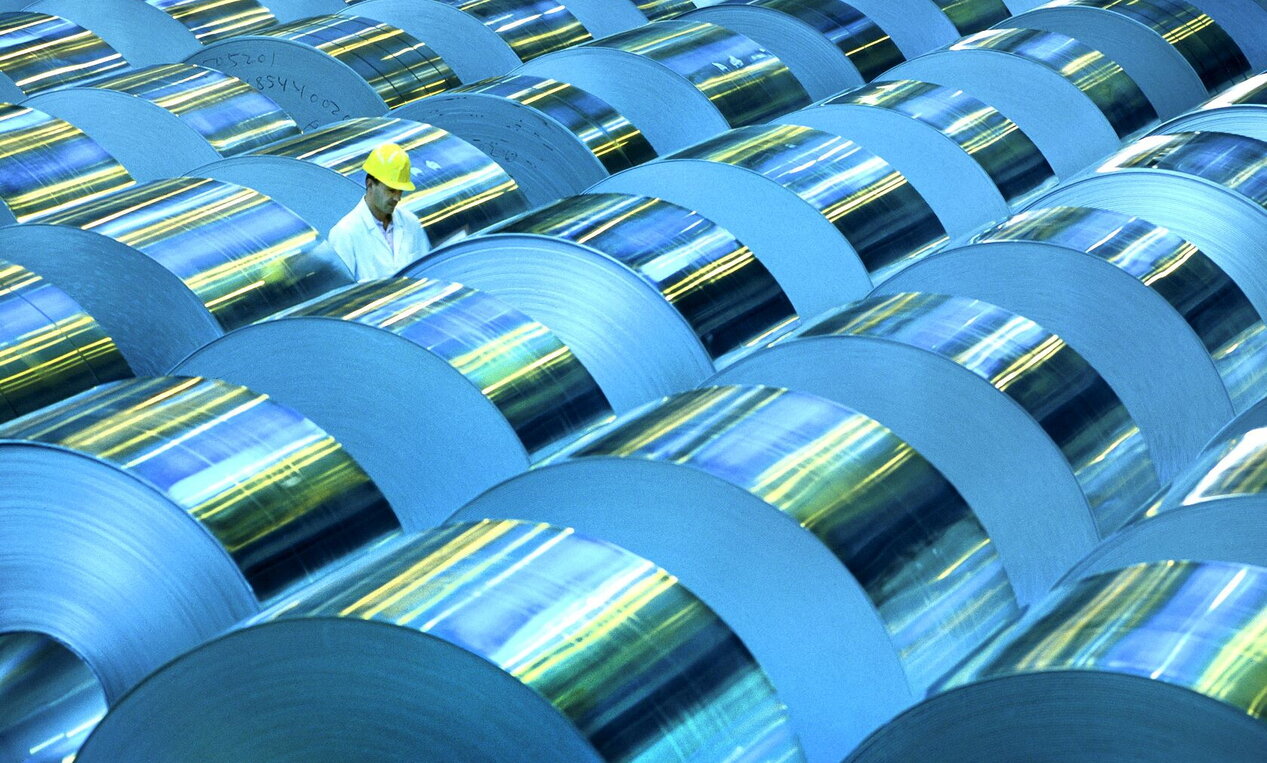
Decarbonization efforts may in themselves lead to increased steel consumption: each new megawatt (MW) of solar power requires 35 to 45 tons of steel, while each new MW of wind power requires 120 to 180 tons. However, the total steel consumption projected in decarbonization scenarios remains relatively modest in absolute terms, amounting to less than 100 tons per year. This figure represents about 5 percent of the estimated total annual steel production and does not account for the steel consumption saved by replacing existing technologies with solar and wind power.
The most widely used material in terms of volume is cement, largely for the construction industry. One short-term strategy for reducing demand is to reduce the proportion of cement in concrete mix by replacing it with other substances that yield less emissions. Other ways to limit the use of cement involve further actions in the building industry: reducing waste, using less material per building, reusing building components where possible, substituting renovation for new construction, improving maintenance, and designing spaces for flexible and shared use.
Technologies and energy sources
Decarbonizing heavy industries, like other sectors, will require a mix of technological solutions and energy sources. Increased electrification, such as using electric arc furnaces in the steel industry, is one avenue. However, generating high-temperature heat with electricity is often not technically or economically feasible. Consequently, alternative solutions to replace current fossil fuels will be necessary.
One option already in use for high-temperature heat production is the exploitation of biological fuels, such as solid biomass and waste, sometimes in co-firing with fossil fuels. Some experts are considering biomethane as a substitute for natural gas, though the industry requires large, concentrated volumes, while biomethane is often produced in small to medium-sized plants distributed across the territory. Different types of waste biomass will need to be used, but these resources are also crucial for decarbonizing other hard-to-abate sectors, such as biofuels for the aviation and maritime industries.
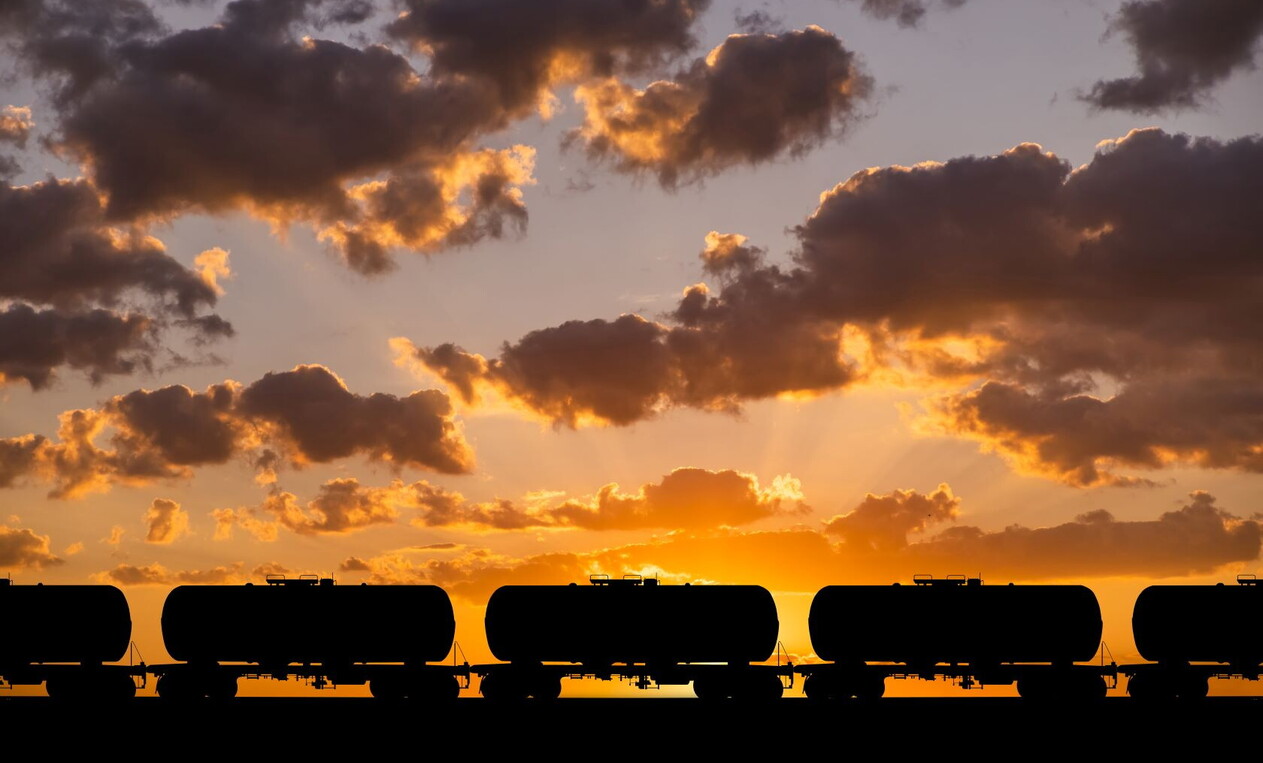
Another energy carrier attracting considerable interest is hydrogen. Hydrogen can be produced cleanly from electrolysis powered by renewable sources (green hydrogen) or from fossil fuels with the capture and storage of the related CO2 emissions (blue hydrogen). Many experts see heavy industry as a sector where hydrogen could play a predominant role, using it to produce high-temperature heat without CO2 emissions as an alternative to fossil fuels. However, significant challenges remain regarding the cost and low efficiency of the hydrogen production and transportation chain. Large-scale use of hydrogen will require substantial investment and long lead times to develop the necessary production and distribution infrastructure.
Currently, heavy industry consumes 53 million tons of hydrogen globally, with 60 percent used for ammonia production, 30 percent for methanol production, and 10 percent in the steel industry. Virtually all of the hydrogen consumed by the industry is produced on-site from fossil fuels, resulting in the emission of 680 million tons of CO2 annually. Even without additional applications, there is already significant demand for hydrogen that could be met by technologies with a lower climate impact than current solutions. Another alternative for high-temperature heat generation is to supplement current fossil-fuel plants with systems to capture and store the CO2 emitted. However, this solution requires additional infrastructure to transport and store the captured CO2, with costs varying significantly depending on the location of the site.
While the use of these alternatives is often technically feasible and can be evaluated on a case-by-case basis, their current costs are not competitive with fossil fuels. As a result, these alternatives remain marginal in an industry characterized by limited margins and significant international competition.
Tools and strategies for decarbonization
One key aspect is the economic value associated with emissions from these processes, which could support the development of zero- or lower-emission alternatives. Several world economies are beginning to develop emissions markets or carbon taxes to stimulate solutions that reduce emissions. However, the current costs per ton of CO2 remain too low to significantly impact these industries. A major barrier is the fear among governments that higher costs would render their industries less competitive globally. Without instruments to level emission costs across different countries, achieving effective measures will be challenging.
One proposed solution is the Carbon Border Adjustment Mechanism (CBAM) developed by the European Commission. CBAM aims to tax the carbon emissions associated with products imported into EU countries, including cement, steel, and fertilizer. The goal is to prevent the relocation of heavy industries to non-EU countries (and the consequent relocation of their emissions) while incentivizing emission reductions in countries exporting to the EU. Although this measure has yet to take effect, it has faced criticism for its potential protectionist effects and the challenges developing countries might face in financing decarbonization solutions for heavy industries.
The infrastructure needed to replace existing technologies must also be considered. Heavy industries involve very large volumes, often concentrated in specific areas, so we need to develop solutions that are scalable. And turning existing assets to low-emission solutions will have to consider the residual technical life of current facilities and the costs of refurbishing them
A global strategy
Heavy industries are among the most challenging sectors to decarbonize, given the limited effectiveness of electrification compared to other end uses. A combination of solutions will likely be necessary due to the variability of industries in this sector and the geographic contexts in which they operate. Supporting these solutions requires the creation of an effective emissions market, possibly at the international level, with well-defined standards that can adapt to the globalized product markets of heavy industries.
National industrial policies often prioritize local economic development, which can conflict with efforts to reduce environmental impact. Therefore, the main challenge is to develop a globally shared strategy that supports emission reductions without penalizing the economic development of countries where these industries are located.